The construction industry has seen significant technological advancements in recent years, with one of the most notable being 3D printing homes. Companies like ICON are leading the charge in this transformative field, with projects such as Lennar's 3D printed homes in Georgetown, Texas, capturing global attention. In this article, we'll explore the concept of 3D printed homes, how they are made, and the advantages they offer over traditional construction methods.
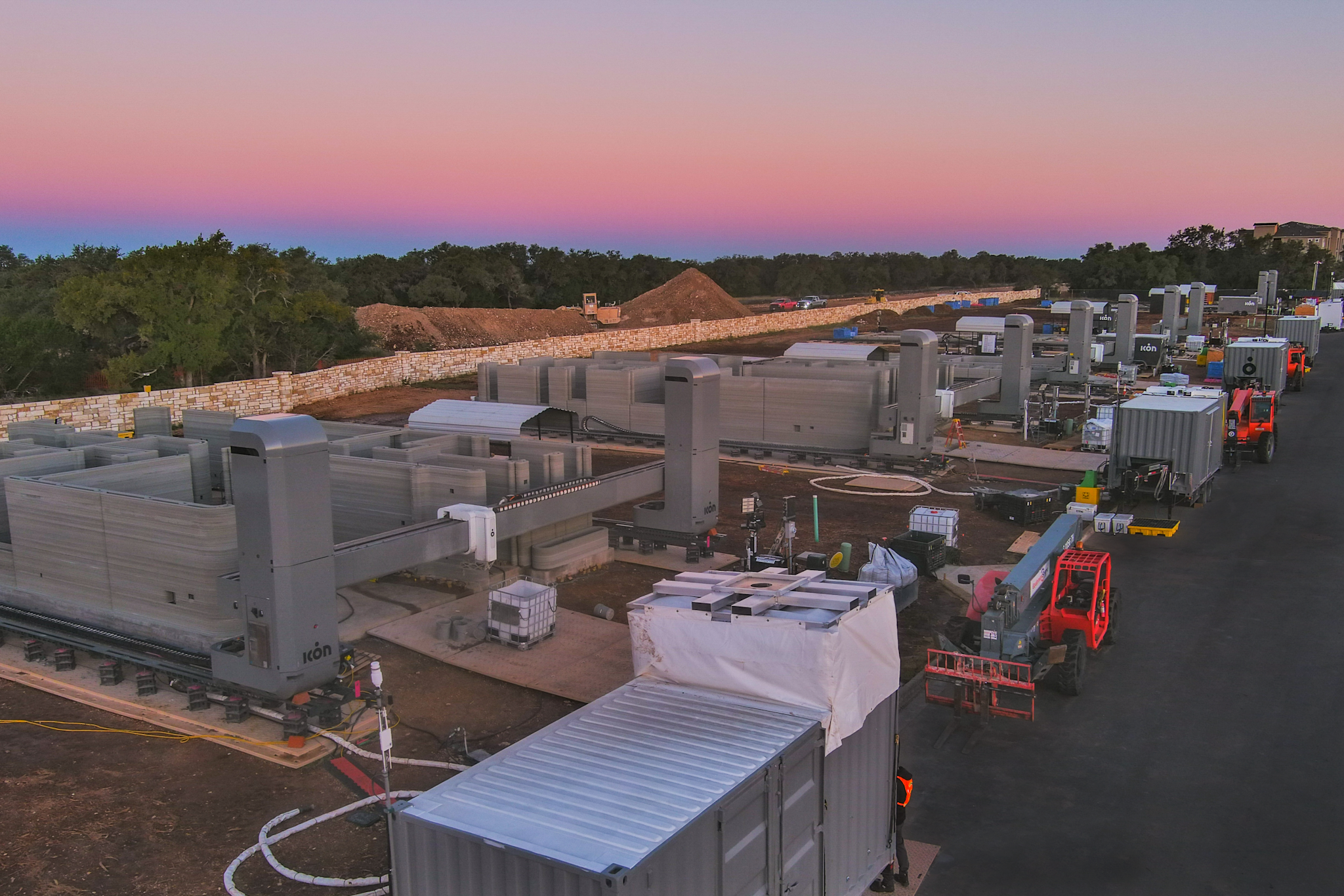
A FLEET OF ICON VULCAN CONSTRUCTION SYSTEMS IS PRINTING THE WALL SYSTEMS FOR THE GENESIS COLLECTION AT WOLF RANCH.
What are 3D Printed Homes?
3D printed homes are residential structures created using large-scale 3D printers that extrude building materials, such as concrete or other composites, layer by layer to form the walls and other architectural elements. This innovative construction technique has the potential to revolutionize the housing industry by drastically reducing construction time, cost, and waste while also offering greater design freedom.
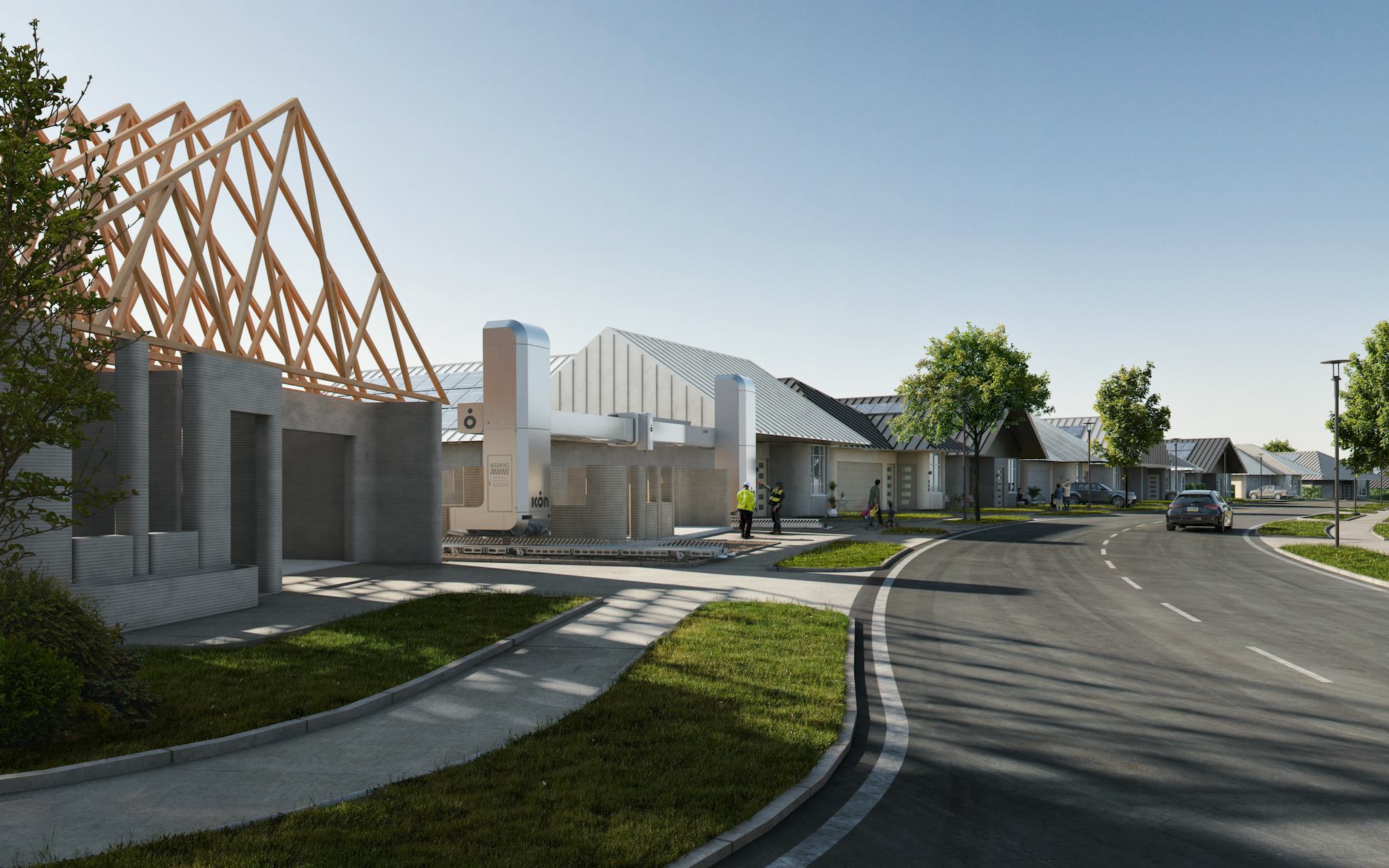
A STREET LEVEL CONCEPT RENDER OF THE GENESIS COLLECTION AT WOLF RANCH.
How Does 3D Printing Homes Work?
The process of 3D printing homes begins with the creation of a digital model of the structure using computer-aided design (CAD) software. This model is then divided into thin layers, which the 3D printer uses as a blueprint to build the structure. The printer, typically mounted on a gantry or robotic arm, extrudes the chosen building material layer by layer, following the pattern provided by the CAD model. The layers then harden and bond together to create the walls and other elements of the home.
Advantages of 3D Printed Homes Over Traditional Construction
1. Speed: One of the most significant benefits of 3D printing homes is the speed at which they can be built. Traditional construction methods may take months to complete, whereas 3D printed homes can be built in a matter of days or weeks, depending on the size and complexity of the design.
2. Cost efficiency: The automated process of 3D printing reduces labor costs and material waste, resulting in more affordable housing options for buyers. Additionally, the reduction in construction time leads to further cost savings.
3. Sustainability: 3D printing homes produce less waste compared to traditional construction methods, as the printer only uses the exact amount of material required for each layer. This not only reduces the overall environmental impact but also contributes to a more sustainable building process.
4. Design freedom: 3D printing technology allows for greater design flexibility, enabling architects and designers to create innovative and unique structures that might be difficult or impossible to achieve with conventional construction methods.
Industry Leaders and Notable Projects
ICON, a Texas-based construction technology company, is at the forefront of the 3D printed home industry. In collaboration with Lennar, one of America's largest homebuilders, ICON is working on a groundbreaking project to build 3D printed homes in Georgetown, Texas at Wolf Ranch. This project aims to demonstrate the viability of 3D printed homes and their potential to address the growing demand for affordable and sustainable housing options.
Conclusion
The 3D printing home industry is poised to disrupt traditional construction methods by offering cost-effective, sustainable, and innovative housing solutions. As the technology continues to advance and more companies like ICON and Lennar champion the cause, the potential for 3D printed homes to transform the housing market is becoming increasingly evident. With benefits such as reduced construction time, lower costs, and greater design freedom, 3D printed homes are likely to become a more prevalent and attractive option for builders and homebuyers alike.
Written by: Texas Roadrunner Realty with ChatGPT
Photo & Video Credit: Icon Build